Home » Wind Turbine » Trends in Wind Turbine Developments
Trends in Wind Turbine Developments
Wind turbine technology has been developed by continuously optimizing turbine design, improving turbine performance, and enhancing overall turbine efficiency. There have been several generations of development and improvement in wind turbine technology, concentrated on blades, generators, direct drive techniques, pitch and yaw control systems, and so on. To provide more electrical energy from wind technology in the next several decades, it requires:
High-power, Large-capacity Wind Turbine
One of the significant developments in wind turbine designing and manufacturing in recent years is the increase in the wind turbine capacity of individual wind turbines. From machines of just 25 kW two decades ago, the commercial range of modern wind turbines sold today is typically 1–6 MW. At the same time, 7–10 MW wind turbines are underway in some larger wind turbine OEMs. With this trend, innovative techniques have been developed and new materials have been adopted for optimizing the wind turbine performance and minimizing the operation and manufacturing costs. Enercon has installed the present world’s largest wind turbine E-126 in Germany and is in the process of installing more units in Belgium. The E-126 turbine is rated at 6 MW with the rotor diameter of 126 m. Clipper Windpower has announced that it is planning to build a 7.5 MW offshore wind turbine.
However, while high-powered wind turbines enable to increase wind power output per unit and lower the cost per kWh, there are some significant challenges facing wind turbine engineers:
To ensure the sustainability of the increase in power output and turbine size, all these challenges must be carefully and effectively addressed.
Offshore Wind Turbine
With several decades of experience with onshore wind technology, offshore wind technology has presently become the focus of the wind power industry. Due to the lower resistance, wind speeds over offshore sea level are typically 20% higher than those over nearby lands. Thus, according to the wind power law, the offshore wind power can capture much more power than the onshore one. This indicates that an offshore wind turbine may gain a higher capacity factor than that of its land-based counterpart. In addition, because the offshore wind speeds are relatively uniform with the lower variations and turbulence, it enables the offshore wind turbines to simplify the control systems and reduces blade and turbine wears.
Sweden installed the first offshore wind turbine in 1990, with the unit capacity of 220 kW. Denmark built its first demonstration offshore wind turbines in 1991, which consists of 11 units, with the unit capacity of 450 kW. With the developments of offshore wind technology in the next several years, offshore wind turbines entered the stage of industrial production in 2001. Today, high capacity wind turbines focus on the offshore application. In 2009, nearly 600 MW offshore wind power were added and connected to electric grids, basically by European countries, bringing the total accumulative installed offshore wind power capacity to more than 2,000 MW. It is expected that in 2010 ten additional European offshore wind farms will be completed to add approximately 1,000 MW online, which represents a growth rate of 75% compared to 2009. The related foundation technologies for offshore applications are also being developed for the erection of higher capacity wind turbines. The annual installed offshore wind power capacities from 1990 to 2009 are shown in Fig. 1.
Offshore wind turbines are installed in seawater, with greater risks of structural corrosion, particularly under conditions of high wave, sea salt splashing and low temperature. To avoid or at least delay the corrosion to protect wind turbines, a number of techniques have been developed. One of them involves the use of electrochemical reactions to prevent the steel corrosion, known as cathodic protection. This is done using a small negative voltage applied to metal. A new method, called impressed current cathodic protection, was invented by Brown and Hefner. This method includes providing an impressed current anode electrochemically coupled to the wind turbine support structure to the impressed current anode to operate the impressed current anode.
In dealing with corrosion control, coating technology plays an important role in the wind power industry. The adoption of high performance of multi-coating systems has achieved satisfactory results to prevent external and internal corrosions of wind turbines. The coating materials used today include thermally sprayed metal (zinc and aluminum), siloxane, acrylic, epoxy, polyurethane, etc. It is expected to develop inorganic hybrid materials (such as polysiloxane) as super durable finishes to meet more aggressive environments.
Floating Wind Turbine
Dr. Sclavounos at MIT is among the first to develop the concept of floating wind turbines in deep water. He and his team in 2004 integrated a wind turbine with a floater. According to their analysis, the floater-mounted turbines could work in water depths of up to 200 m.
The world’s first commercial-scale floating wind turbine has being constructed in deep water far from land. The turbine is mounted on a floating turbine platform on the sea surface and anchored to the seabed with three strong chains. Changing the length of the chains could allow the turbine to operate in water depths between 50 and 300 m, enough to take it far out into the deep ocean. By comparing with existing offshore wind turbines, floating wind turbine is more economic in the installation and shipping. Electricity would be sent ashore using undersea cables.
Sway, a Norwegian company, plans to launch its prototype of floating wind turbines in 2010. The turbine is to be mounted on an elongated floating mast, connected to the seabed by a metal tube. The turbine mast is designed to sway with wind and waves, and can lean at an angle of up to 15°.
Drivetrain
In a geared wind turbine, the term “drivetrain” usually encompasses all rotating parts, from the rotor hub, the main gearbox, to the generator. The main gearbox is one of the most important components in the wind turbine, for increasing the slow rotation speed of the blades to the desired high speed of the generator’s rotor. It is also the most expensive component in the turbine and can easily fail before reaching the intended life. With the increase in the turbine size and capacity in the last decade, the gearbox has been subjected to even greater loads and stresses. There are significant challenges presented to gearbox designers and manufacturers.
Wind turbines typically use planetary gears to divide torque along three paths and reduce individual loads on each gear. However, torsional loads twist gears out of alignment, and slight dimensional variation in gearbox components, indicate that planetary gears do not equally share the load. Misaligned gears, shock loads, and uneven forces lead to highly localized stress and eventually fracture along the gear edges. To solve these problems, an innovative type of gearbox has been developed (Fig. 2), using the Integrated Flex-pin Bearing (IFB) to equalize gear loads, eliminate misalignment, and dramatically improve wind turbine reliability. This novel design increases torque capacity of planetary gears up to 50%.
Based on the failure analysis of gearboxes, the Gearbox Reliability Collaborative initiated at US National Renewable Energy Laboratory (NREL) provides a fresh approach toward better gearboxes that combines the resources of key members of the supply chain to investigate design-level root causes of field problems and solutions that will lead to higher gearbox reliability.
- Developing innovative techniques;
- Decreasing wind turbine costs through technology advancement;
- Optimizing manufacturing processes and enhancing manufacturing operations;
- Improving wind turbine performance and efficiency;
- Reducing operating and maintenance costs;
- Expanding wind turbine production capacities.
High-power, Large-capacity Wind Turbine
One of the significant developments in wind turbine designing and manufacturing in recent years is the increase in the wind turbine capacity of individual wind turbines. From machines of just 25 kW two decades ago, the commercial range of modern wind turbines sold today is typically 1–6 MW. At the same time, 7–10 MW wind turbines are underway in some larger wind turbine OEMs. With this trend, innovative techniques have been developed and new materials have been adopted for optimizing the wind turbine performance and minimizing the operation and manufacturing costs. Enercon has installed the present world’s largest wind turbine E-126 in Germany and is in the process of installing more units in Belgium. The E-126 turbine is rated at 6 MW with the rotor diameter of 126 m. Clipper Windpower has announced that it is planning to build a 7.5 MW offshore wind turbine.
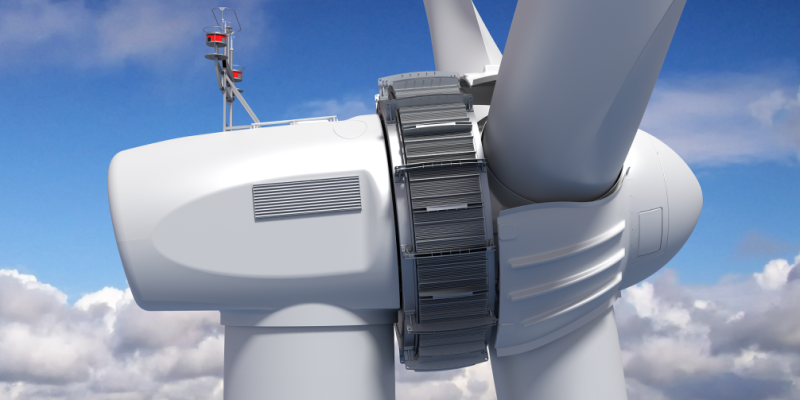
However, while high-powered wind turbines enable to increase wind power output per unit and lower the cost per kWh, there are some significant challenges facing wind turbine engineers:
a. Failure rates of wind turbines depend not only on turbines’ operational age but also their rated power. High-power, large-size wind turbines have shown significant higher annual failure rates due to the primary failures of the control system, drivetrain, and electronic/electrical components. Because most of mega-watt wind turbines were usually among the first models installed, they show high early failure rates that decrease slightly throughout their years of operation.
b. Wind velocity is proportional to the height from the earth’s surface. With the continuously increasing blade length of large wind turbines, the differences of the dynamic wind loads between the rotating blades become significantly large, resulting in a large resultant unbalanced fatigue load on the turbine blades, and a resultant unbalanced torsional moment on the main shaft, and in turn, on the wind tower.
c. During wind turbine’s operation, a minimum clearance must be maintained between the blade tips and the wind tower. Therefore, high blade stiffness is required to avoid the collision between the blades and the tower. In practice, the maximum blade length is constrained by required stiffness and stresses of blades.
d. Large wind turbines become more susceptible to variations in wind speed and intensity across the swept area.
e. Transportation and installation of long-length blades remain challenges to the wind power industry. The length of a blade for a 4.5–5 MW wind turbine ranges 50–70 m. It is very difficult to ship such long blades through current highways and installed on the top of 120–160 m wind towers.
f. The tower strength is another consideration. For a given survivable wind speed, the mass of a wind turbine is approximately proportional to the cube of its blade length and the output power is proportional to the square of it blade length. Typically, the mass of a 4.5–5 MW is of 200–500 tons. It was reported that doubling the tower height generally requires doubling the diameter as well, increasing the amount of material by a factor of 8.
To ensure the sustainability of the increase in power output and turbine size, all these challenges must be carefully and effectively addressed.
Offshore Wind Turbine
With several decades of experience with onshore wind technology, offshore wind technology has presently become the focus of the wind power industry. Due to the lower resistance, wind speeds over offshore sea level are typically 20% higher than those over nearby lands. Thus, according to the wind power law, the offshore wind power can capture much more power than the onshore one. This indicates that an offshore wind turbine may gain a higher capacity factor than that of its land-based counterpart. In addition, because the offshore wind speeds are relatively uniform with the lower variations and turbulence, it enables the offshore wind turbines to simplify the control systems and reduces blade and turbine wears.
Sweden installed the first offshore wind turbine in 1990, with the unit capacity of 220 kW. Denmark built its first demonstration offshore wind turbines in 1991, which consists of 11 units, with the unit capacity of 450 kW. With the developments of offshore wind technology in the next several years, offshore wind turbines entered the stage of industrial production in 2001. Today, high capacity wind turbines focus on the offshore application. In 2009, nearly 600 MW offshore wind power were added and connected to electric grids, basically by European countries, bringing the total accumulative installed offshore wind power capacity to more than 2,000 MW. It is expected that in 2010 ten additional European offshore wind farms will be completed to add approximately 1,000 MW online, which represents a growth rate of 75% compared to 2009. The related foundation technologies for offshore applications are also being developed for the erection of higher capacity wind turbines. The annual installed offshore wind power capacities from 1990 to 2009 are shown in Fig. 1.
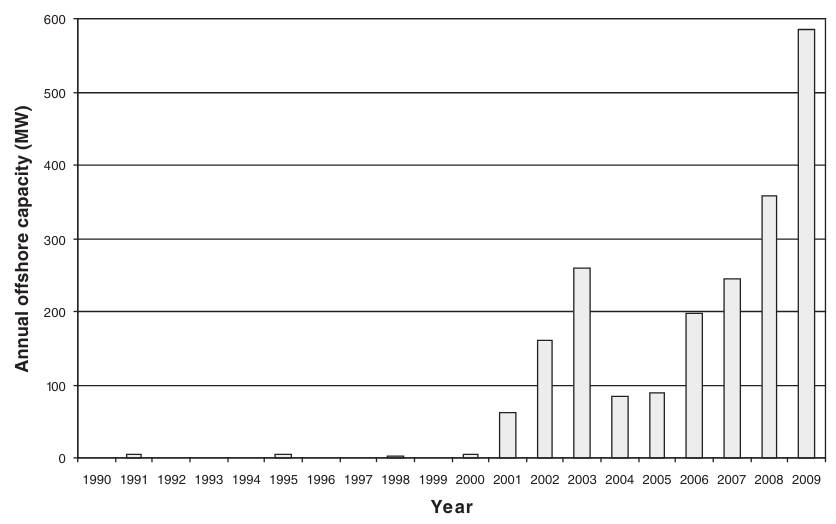
Figure 1
Offshore wind turbines are installed in seawater, with greater risks of structural corrosion, particularly under conditions of high wave, sea salt splashing and low temperature. To avoid or at least delay the corrosion to protect wind turbines, a number of techniques have been developed. One of them involves the use of electrochemical reactions to prevent the steel corrosion, known as cathodic protection. This is done using a small negative voltage applied to metal. A new method, called impressed current cathodic protection, was invented by Brown and Hefner. This method includes providing an impressed current anode electrochemically coupled to the wind turbine support structure to the impressed current anode to operate the impressed current anode.
In dealing with corrosion control, coating technology plays an important role in the wind power industry. The adoption of high performance of multi-coating systems has achieved satisfactory results to prevent external and internal corrosions of wind turbines. The coating materials used today include thermally sprayed metal (zinc and aluminum), siloxane, acrylic, epoxy, polyurethane, etc. It is expected to develop inorganic hybrid materials (such as polysiloxane) as super durable finishes to meet more aggressive environments.
Floating Wind Turbine
Dr. Sclavounos at MIT is among the first to develop the concept of floating wind turbines in deep water. He and his team in 2004 integrated a wind turbine with a floater. According to their analysis, the floater-mounted turbines could work in water depths of up to 200 m.
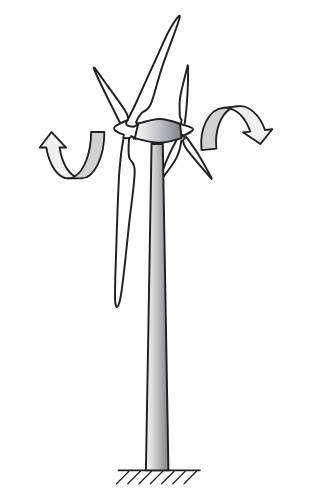
The world’s first commercial-scale floating wind turbine has being constructed in deep water far from land. The turbine is mounted on a floating turbine platform on the sea surface and anchored to the seabed with three strong chains. Changing the length of the chains could allow the turbine to operate in water depths between 50 and 300 m, enough to take it far out into the deep ocean. By comparing with existing offshore wind turbines, floating wind turbine is more economic in the installation and shipping. Electricity would be sent ashore using undersea cables.
Sway, a Norwegian company, plans to launch its prototype of floating wind turbines in 2010. The turbine is to be mounted on an elongated floating mast, connected to the seabed by a metal tube. The turbine mast is designed to sway with wind and waves, and can lean at an angle of up to 15°.
Drivetrain
In a geared wind turbine, the term “drivetrain” usually encompasses all rotating parts, from the rotor hub, the main gearbox, to the generator. The main gearbox is one of the most important components in the wind turbine, for increasing the slow rotation speed of the blades to the desired high speed of the generator’s rotor. It is also the most expensive component in the turbine and can easily fail before reaching the intended life. With the increase in the turbine size and capacity in the last decade, the gearbox has been subjected to even greater loads and stresses. There are significant challenges presented to gearbox designers and manufacturers.
Wind turbines typically use planetary gears to divide torque along three paths and reduce individual loads on each gear. However, torsional loads twist gears out of alignment, and slight dimensional variation in gearbox components, indicate that planetary gears do not equally share the load. Misaligned gears, shock loads, and uneven forces lead to highly localized stress and eventually fracture along the gear edges. To solve these problems, an innovative type of gearbox has been developed (Fig. 2), using the Integrated Flex-pin Bearing (IFB) to equalize gear loads, eliminate misalignment, and dramatically improve wind turbine reliability. This novel design increases torque capacity of planetary gears up to 50%.
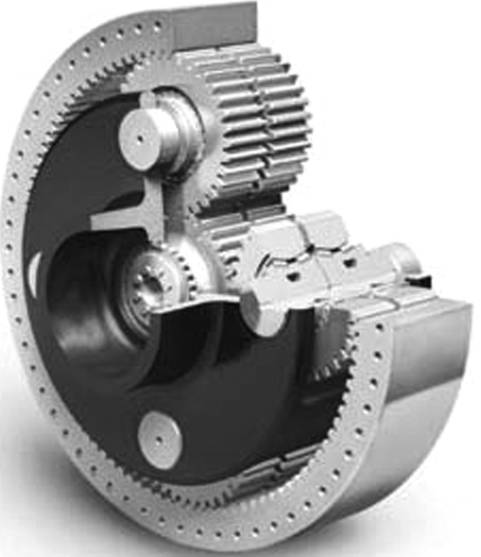
Figure 2
Based on the failure analysis of gearboxes, the Gearbox Reliability Collaborative initiated at US National Renewable Energy Laboratory (NREL) provides a fresh approach toward better gearboxes that combines the resources of key members of the supply chain to investigate design-level root causes of field problems and solutions that will lead to higher gearbox reliability.
Post a Comment:
You may also like:
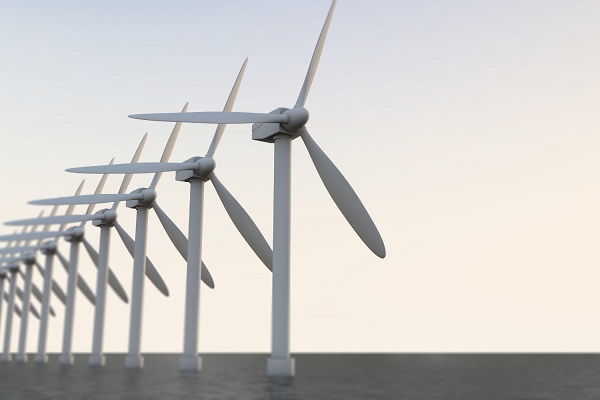
Featured Articles
Horizontal Axis vs. Vertical Axis
Wind turbines are machines that generate electricity from the kinetic energy of the wind. In history, they were more ...
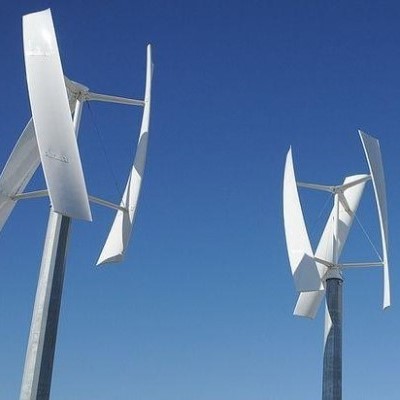
Wind Turbine Glossary
Wind energy is the kinetic energy that is present in moving air. The amount of potential energy depends mainly on wind speed, but ...

Household Wind Energy System Components
Basic parts of home wind energy systems generally comprise a rotor, a generator or alternator mounted on a frame, a tail ...
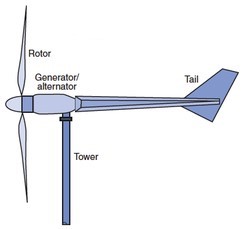
Horizontal Axis Wind Turbine Design
Today, the most common design of wind turbine is the horizontal axis wind turbine (HAWT). That is, the axis of rotation is ...
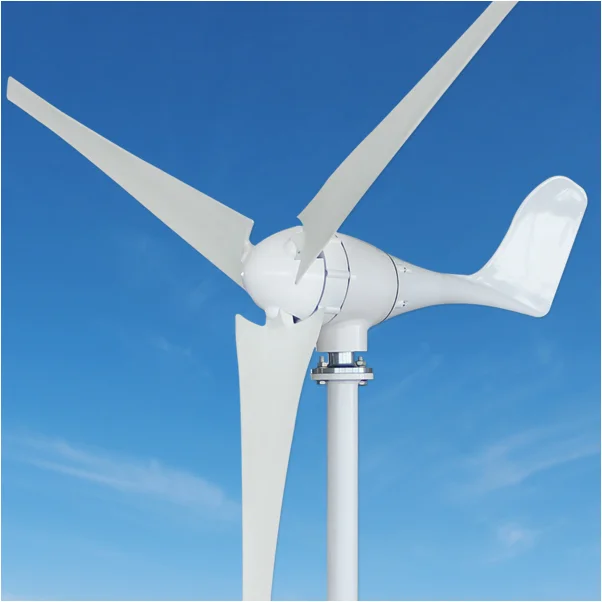
Overvoltage Protection for Wind ...
Due to their principle of operation, wind turbines have to be set up outdoors and are used in a wide range of ...
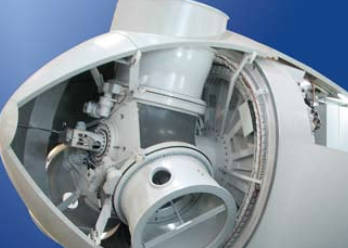