Home » Wind Turbine » Wind Turbine Controls
Wind Turbine Controls
Wind turbine control systems continue to play important roles for ensuring wind turbine reliable and safe operation and to optimize wind energy capture. The main control systems in a modern wind turbine include pitch control, stall control (passive and active), yaw control, and others.
Under high wind speed conditions, the power output from a wind turbine may exceed its rated value. Thus, power control is required to control the power output within allowable fluctuations for avoiding turbine damage and stabilizing the power output. There are two primary control strategies in the power control: pitch control and stall control. The wind turbine power control system is used to control the power output within allowable fluctuations.
Pitch Control
The pitch control system is a vital part of the modern wind turbine. This is because the pitch control system not only continually regulates the wind turbine's blade pitch angle to enhance the efficiency of wind energy conversion and power generation stability, but also serves as the security system in case of high wind speeds or emergency situations. It requires that even in the event of grid power failure, the rotor blades can be still driven into their feathered positions by using either the power of backup batteries or capacitors or mechanical energy storage devices.
Early techniques of active blade pitch control applied hydraulic actuators to control all blades together. However, these collective pitch control techniques could not completely satisfy all requirements of blade pitch angle regulation, especially for MW wind turbines with the increase in blade length and hub height. This is because wind is highly turbulent flow and the wind speed is proportional to the height from the ground. Therefore, each blade experiences different loads at different rotation positions. As a result, more superior individual blade pitch control techniques have been developed and implemented, allowing control of asymmetric aerodynamic loads on the blades, as well as structural loads in the non-rotating frame such as tower side-side bending. In such a control system, each blade is equipped with its own pitch actuator, sensors and controller.
In today’s wind power industry, there are primarily two types of blade pitch control systems: hydraulic controlled and electric controlled systems. As shown in Figure 1, the hydraulic pitch control system uses a hydraulic actuator to drive the blade rotating with respect to its axial centreline. The most significant advantages of hydraulic pitch control system include its large driving power, lack of a gearbox, and robust backup power. Due to these advantages, hydraulic pitch control systems historically dominate wind turbine control in Europe and North America for many years.
The electric pitch control systems have been developed alternatively with the hydraulic systems. This type of control system has a higher efficiency than that of hydraulic controlled systems (which is usually less than 55%) and avoids the risk of environmental pollution due to hydraulic fluid being split or leaked.
In an electric pitch control system as shown in Figure 2, the motor connects to a gearbox to lower the motor speed to a desired control speed. A drive pinion gear engages with an internal ring gear, which is rigidly attached to the roof of the rotor blade. Alternatively, some wind turbine manufacturers use the belt-drive structure adjusting the pitch angle. The use of electric motors can raise the responsiveness rate and sensitivity of blade pitch control. To enhance operation reliability, the use of redundant pitch control systems was proposed to be equipped in large wind turbines.
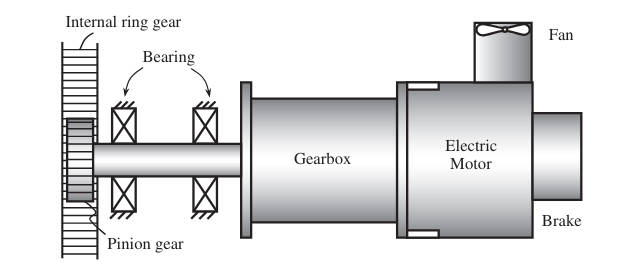
Figure 2
Stall Control
Besides pitch control, stall control is another approach for controlling and protecting wind turbines. The concept of stall control is that the power is regulated through stalling the blades after rated speed is achieved.
Stall control can be further divided into passive and active control approaches. Passive stall control is basically used in wind turbines in which the blades are bolted to the hub at a fixed installing angle. In a passive stall-regulated wind turbine, the power regulation relies on the aerodynamic features of blades. In low and moderate wind speeds, the turbine operates near maximum efficiency. At high wind speeds, the turbine is automatically controlled by means of stalled blades to limit the rotational speed and power output, protecting the turbine from excessive wind speeds.
Compared with pitch control, a passive stall control system has a simple structure and avoids using a complex control system, leading to high reliability of the control system. In addition, the power fluctuations are lower for stall-regulated turbines. However, this control method has some disadvantages, such as lower efficiency, the requirement of external equipment at the turbine start, larger dynamic loads acting on the blades, nacelle, and tower, dependence on reliable brakes for the operation safety. Therefore, this control technique has been primarily used for small and medium wind turbines. Since the capacity of wind turbines has entered the multi-megawatt power range in recent years, pitch control has become dominant in the wind power market.
The active stall control technique has been developed for large wind turbines. An active stall wind turbine has stalling blades together with a blade pitch system. Since the blades at high wind speeds are turned towards stall, in the opposite direction as with pitch-control systems, this control method is also referred to as negative pitch control. Compared with passive stall control, active control provides more accurate control on the power output and maintains the rated power at high wind speeds. However, with the addition of the pitch-control mechanism, the active stall control mode increases the turbine cost and decreases operation reliability.
With megawatt wind turbines becoming the mainstream in the wind power industry from the late 1990s, pitch control is more favorable than stall control. It has been reported that the number of pitch-regulated turbines is four times higher than that of stall-regulated turbines and the trend is going to continue in coming decades.
Yaw Control
In order to maximize the wind power output and minimize the asymmetric loads acting on the rotor blades and the tower, a horizontal-axis wind turbine must be oriented with rotor against the wind by using an active yaw control system. Like wind pitch systems, yaw systems can be driven either electrically or hydraulically. Generally, hydraulic yaw systems were used in the earlier time of the wind turbine development. In modern wind turbines, yaw control is done by electric motors. The yaw control system usually consists of an electrical motor with a speed reducing gearbox, a bull gear which is fixed to the tower, a wind vane to gain the information about wind direction, a yaw deck, and a brake to lock the turbine securely in yaw when the required position is reached. For a large wind turbine with high driving loads, the yaw control system may use two or more yaw motors to work together for driving a heavy nacelle (see Figure 3).
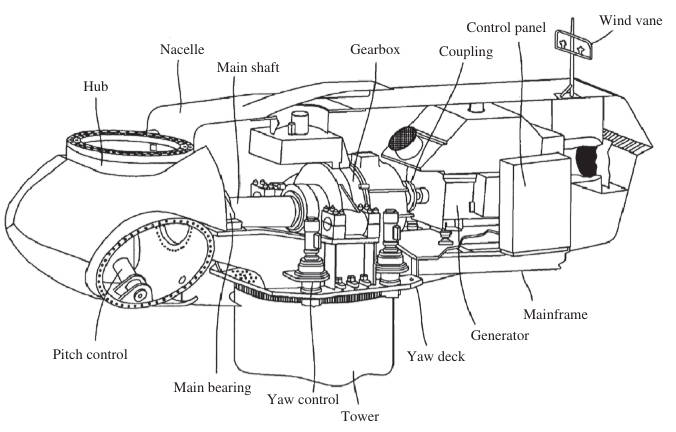
Figure 3
In practice, the yaw error signals obtained from the wind vane are used to calculate the average yaw angle in a short interval. When this average yaw angle exceeds the preset threshold, the yaw motor is activated to align the turbine with the wind direction. Thus, with heavily filtered wind direction measurements, the actions of yaw control are rather limited and slow.
Other Control Approaches
In the early time of wind turbine design, ailerons were once used to control the power output. This method involves placing moveable flaps on the trailing edge of rotor blades. The ailerons change the lift and drag characteristics of the blades and eventually change the rotor torque, which enable to regulate rotor speed and rotor power output. However, this method was less successful and was soon abandoned.
Another possibility is to yaw the rotor partly out of the wind to decrease power. This technique of yaw control is in practice used only for tiny wind turbines (>1 kW).
Under high wind speed conditions, the power output from a wind turbine may exceed its rated value. Thus, power control is required to control the power output within allowable fluctuations for avoiding turbine damage and stabilizing the power output. There are two primary control strategies in the power control: pitch control and stall control. The wind turbine power control system is used to control the power output within allowable fluctuations.
Pitch Control
The pitch control system is a vital part of the modern wind turbine. This is because the pitch control system not only continually regulates the wind turbine's blade pitch angle to enhance the efficiency of wind energy conversion and power generation stability, but also serves as the security system in case of high wind speeds or emergency situations. It requires that even in the event of grid power failure, the rotor blades can be still driven into their feathered positions by using either the power of backup batteries or capacitors or mechanical energy storage devices.
Early techniques of active blade pitch control applied hydraulic actuators to control all blades together. However, these collective pitch control techniques could not completely satisfy all requirements of blade pitch angle regulation, especially for MW wind turbines with the increase in blade length and hub height. This is because wind is highly turbulent flow and the wind speed is proportional to the height from the ground. Therefore, each blade experiences different loads at different rotation positions. As a result, more superior individual blade pitch control techniques have been developed and implemented, allowing control of asymmetric aerodynamic loads on the blades, as well as structural loads in the non-rotating frame such as tower side-side bending. In such a control system, each blade is equipped with its own pitch actuator, sensors and controller.
In today’s wind power industry, there are primarily two types of blade pitch control systems: hydraulic controlled and electric controlled systems. As shown in Figure 1, the hydraulic pitch control system uses a hydraulic actuator to drive the blade rotating with respect to its axial centreline. The most significant advantages of hydraulic pitch control system include its large driving power, lack of a gearbox, and robust backup power. Due to these advantages, hydraulic pitch control systems historically dominate wind turbine control in Europe and North America for many years.
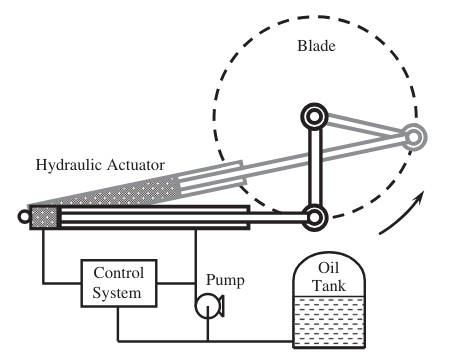
Figure 1
The electric pitch control systems have been developed alternatively with the hydraulic systems. This type of control system has a higher efficiency than that of hydraulic controlled systems (which is usually less than 55%) and avoids the risk of environmental pollution due to hydraulic fluid being split or leaked.
In an electric pitch control system as shown in Figure 2, the motor connects to a gearbox to lower the motor speed to a desired control speed. A drive pinion gear engages with an internal ring gear, which is rigidly attached to the roof of the rotor blade. Alternatively, some wind turbine manufacturers use the belt-drive structure adjusting the pitch angle. The use of electric motors can raise the responsiveness rate and sensitivity of blade pitch control. To enhance operation reliability, the use of redundant pitch control systems was proposed to be equipped in large wind turbines.
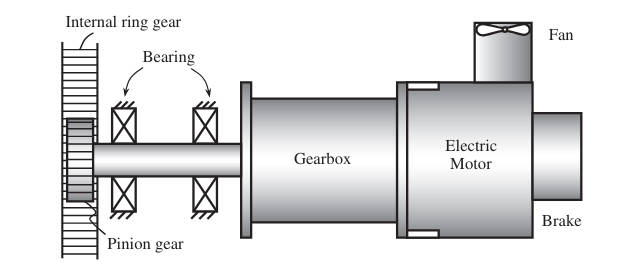
Figure 2
Besides pitch control, stall control is another approach for controlling and protecting wind turbines. The concept of stall control is that the power is regulated through stalling the blades after rated speed is achieved.
Stall control can be further divided into passive and active control approaches. Passive stall control is basically used in wind turbines in which the blades are bolted to the hub at a fixed installing angle. In a passive stall-regulated wind turbine, the power regulation relies on the aerodynamic features of blades. In low and moderate wind speeds, the turbine operates near maximum efficiency. At high wind speeds, the turbine is automatically controlled by means of stalled blades to limit the rotational speed and power output, protecting the turbine from excessive wind speeds.
Compared with pitch control, a passive stall control system has a simple structure and avoids using a complex control system, leading to high reliability of the control system. In addition, the power fluctuations are lower for stall-regulated turbines. However, this control method has some disadvantages, such as lower efficiency, the requirement of external equipment at the turbine start, larger dynamic loads acting on the blades, nacelle, and tower, dependence on reliable brakes for the operation safety. Therefore, this control technique has been primarily used for small and medium wind turbines. Since the capacity of wind turbines has entered the multi-megawatt power range in recent years, pitch control has become dominant in the wind power market.
The active stall control technique has been developed for large wind turbines. An active stall wind turbine has stalling blades together with a blade pitch system. Since the blades at high wind speeds are turned towards stall, in the opposite direction as with pitch-control systems, this control method is also referred to as negative pitch control. Compared with passive stall control, active control provides more accurate control on the power output and maintains the rated power at high wind speeds. However, with the addition of the pitch-control mechanism, the active stall control mode increases the turbine cost and decreases operation reliability.
With megawatt wind turbines becoming the mainstream in the wind power industry from the late 1990s, pitch control is more favorable than stall control. It has been reported that the number of pitch-regulated turbines is four times higher than that of stall-regulated turbines and the trend is going to continue in coming decades.
Yaw Control
In order to maximize the wind power output and minimize the asymmetric loads acting on the rotor blades and the tower, a horizontal-axis wind turbine must be oriented with rotor against the wind by using an active yaw control system. Like wind pitch systems, yaw systems can be driven either electrically or hydraulically. Generally, hydraulic yaw systems were used in the earlier time of the wind turbine development. In modern wind turbines, yaw control is done by electric motors. The yaw control system usually consists of an electrical motor with a speed reducing gearbox, a bull gear which is fixed to the tower, a wind vane to gain the information about wind direction, a yaw deck, and a brake to lock the turbine securely in yaw when the required position is reached. For a large wind turbine with high driving loads, the yaw control system may use two or more yaw motors to work together for driving a heavy nacelle (see Figure 3).
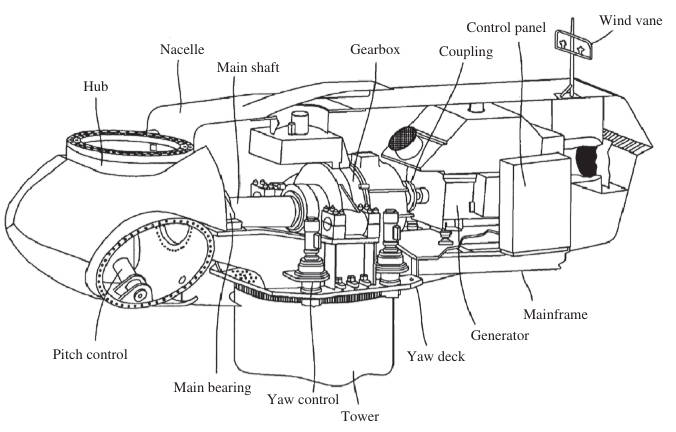
Figure 3
In practice, the yaw error signals obtained from the wind vane are used to calculate the average yaw angle in a short interval. When this average yaw angle exceeds the preset threshold, the yaw motor is activated to align the turbine with the wind direction. Thus, with heavily filtered wind direction measurements, the actions of yaw control are rather limited and slow.
Other Control Approaches
In the early time of wind turbine design, ailerons were once used to control the power output. This method involves placing moveable flaps on the trailing edge of rotor blades. The ailerons change the lift and drag characteristics of the blades and eventually change the rotor torque, which enable to regulate rotor speed and rotor power output. However, this method was less successful and was soon abandoned.
Another possibility is to yaw the rotor partly out of the wind to decrease power. This technique of yaw control is in practice used only for tiny wind turbines (>1 kW).
Post a Comment:
You may also like:
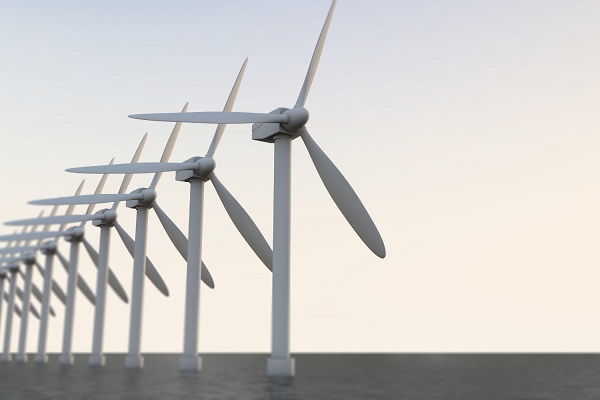
Featured Articles
Horizontal Axis vs. Vertical Axis
Wind turbines are machines that generate electricity from the kinetic energy of the wind. In history, they were more ...
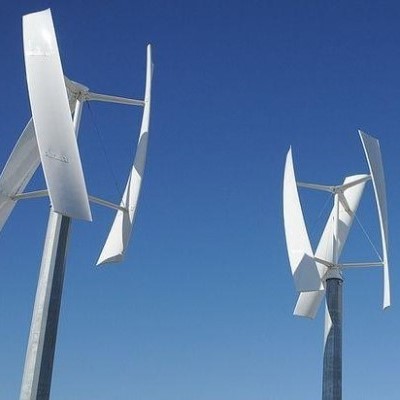
Horizontal Axis Wind Turbine Design
Today, the most common design of wind turbine is the horizontal axis wind turbine (HAWT). That is, the axis of rotation is ...
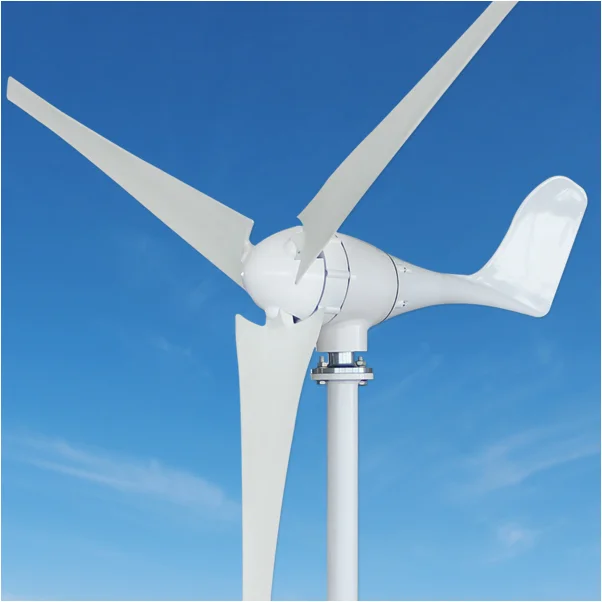
Overvoltage Protection for Wind ...
Due to their principle of operation, wind turbines have to be set up outdoors and are used in a wide range of ...
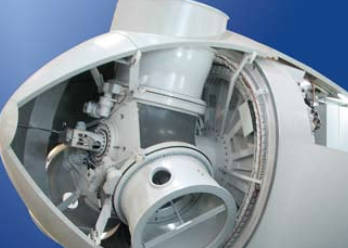
What is a Wind Turbine?
Wind turbines are devices that convert the kinetic energy from the wind into mechanical power, which can then be used to generate ...
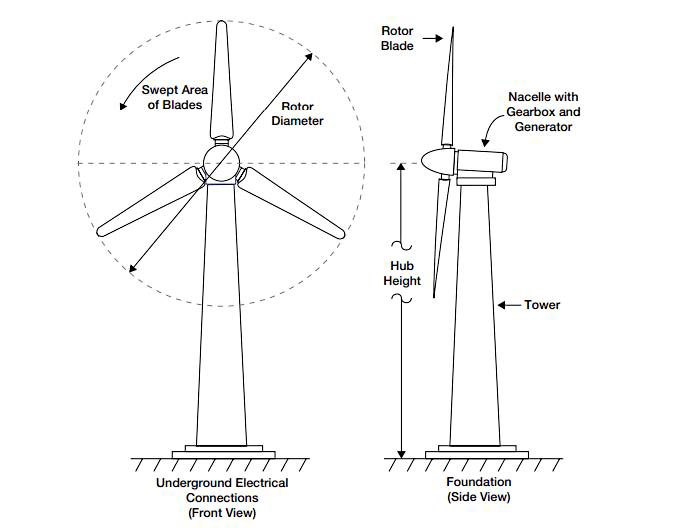
Wind Turbine Glossary
Wind energy is the kinetic energy that is present in moving air. The amount of potential energy depends mainly on wind speed, but ...
